Kum Döküm
Model Tasarımında Dikkat Edilecek Hususlar
a- İmalat (Konstrüksiyon)
resmi en iyi biçimde okunarak modelin hatasız yapılması
sağlanmalıdır. Döküm parçasının ölçü tamlığı ve sağlıklı
kalıplanabilmesi modelin ölçü tamlığına ve teknolojik kurallara
göre yapılmasına bağlıdır.
b- Modelci ekonomik kalıplama metodunu bulmak ve buna göre
çalışmak zorundadır.Modeli basit ve kısa zamanda yapacak şekilde
tasarlamalıdır.
c- Modeli elde veya makinede kalıplayacak eleman kalifiye olmasa
bile hatasız kalıplayabileceği bir şekilde düzenlenmelidir.
d- Kalıp düzenlenmesi öyle olmalıdır' ki ergimiş maden yapılmış
kalıp içine kolaylıkla aksın ve hatasız katılaşsın.
e- Dökümden sonra kalıp içerisinde hava boşluğu ve curuf
kalmayacak şekilde dizayn edilmelidir.
1- Mala yüzeyi seçimi:
Mala yüzeyi:Kalıbın ayrılma yüzeyine mala yüzeyi denir. Mala
yüzeyi kalıbın açılarak modelin kalıbın içerisinden çıkmasını
temin eder. Mala yüzeyinin modelin hatasız kalıplanmasını temin
edecek yüzeyden veya yüzeylerden seçilmesine dikkat edilmelidir.
Ayrıca mala yüzeyi seçiminde parçanın şekli kalıplama tekniği
ile kalıplama sayısının' da önemi büyüktür.
2- Kalıplama
sayısı:
Az sayıda kalıplanacak modeller genellikle ahşap malzemelerden
ve el işçiliği ile kalıplanacak tarzda yapılır. Model en hatasız
ve en ekonomik kalıplamayı sağlayacak tarzda mala yüzeyi seçilir
ve gerekiyorsa model mala yüzeyinden parçalı yapılır.
Çok sayıda kalıplanacak modeller (seri üretim modelleri)
genellikle plakaya bir veya birden fazla model bağlanarak elde
veya kalıplama makinelerinde kalıplanırlar. Bu modeller
genellikle metal veya polimer malzemelerden yapılırlar,
plakaları ise kontrplak, alüminyum veya dökme demirden
yapılırlar.
3-Kalıplanma
şekli:
Modeller yapılırken kalıplama yapacak dökümhanenin teknik
imkanları ve kalıplanma teknolojisi göz önünde
bulundurulmalıdır.
a- Elde kalıplama: Modellerin metal veya yine modelcinin yaptığı
derecelerle kum ile kalıplanma işlemidir. Genellikle kupol veya
indiksiyon ocaklarında ergitilen maden kum kalıplara dökülür.
b-Makinede kalıplama: Plakalara bağlanmış seri üretim
modellerinin standard derecelerle normal basınçlı kalıplama
makineleri ile kalıplanması işlemidir. Bu işlem yüksek basınçlı
kalıplama makineleri ile daha seri ve hatasız olarak yapılır.
Dizamatik sistemle çalışan dökümhanelerde kalıplanma işlemi son
derece hızlı ve hatasız olur.
Model
ilaveleri:
1- Eğim: Modelin kalıplandıktan sonra kalıbı bozmadan kalıbın
içerisinden çıkarılabilmesi için mala yüzeyine dik olan
yüzeylere verilen açıdır.bu açı tek yüzeylere verildiğinde eğim
karşılıklı (silindirik) yüzeylere verildiğinde koniklik adini
alır.
Modele üç türlü eğim verilebilir bunlar:
1-Artı Eğim: Eğim açısı veya % miktarı modelin üzerine fazlalık
olarak verilir.
2- Eksi eğim:Açısı veya % miktarı model ölçüsünden eksilterek
verilir.
3- Ortalama eğim: Model yüzeyine yüksekliğin yarısında ilave
yarısından sonra eksilterek verilir.
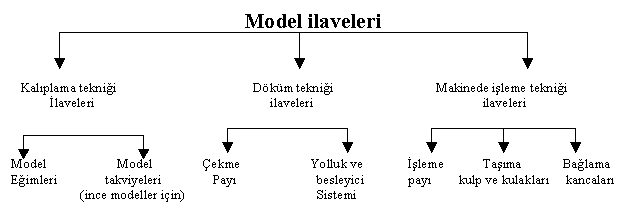
Eğim ve koniklikler DIN e göre standard olup
tabloda gösterilmiştir
Model
eğimleri:
YÜKSEKLİK
(mm) |
EĞİM
(Derece) |
YÜKSEKLİK
(mm) |
EĞİM
(mm) |
10'a
kadar |
3 |
250'ye
kadar |
1,5 |
15'e
kadar |
2 |
320'ye
kadar |
2 |
30'a
kadar |
1.30 |
500'e
kadar |
3 |
50'ye
kadar |
1 |
800'e
kadar |
4,5 |
80'e
kadar |
0.45 |
1200'e
kadar |
7 |
180'e
kadar |
0.30 |
2000'e
kadar |
11 |
|
|
4000'e
kadar |
21 |
Eğimlerin
yarar ve zararları: Modele verilen aşırı eğim parçanın resme
göre şeklini bozar ayrıca parçanın yerinde çalışmasına engel
olabileceği düşünülmelidir. Modele az verilen eğim ise modelim
kumdan çıkmasını güçlendireceğinden dolayı fazla takalamaya
ihtiyaç gösterir bu aşırı takalama ölçü değişikliğine yol açar.
Çekme: Kalıba yüksek ısıda dökülen maden soğuma esnasında
hacimce küçülmeye maruz kalır buna çekme denir.
Çekmeyi ölçülerde meydana gelen küçülme ve kütlede meydana gelen
küçülme olmak üzere ikiye ayırabiliriz. Her malzemenin çekme
oranı farklıdır bu oran % olarak 100 mm de .....mm cinsinden
ilave edilir. Örneğin dökme demir %1 çeker dolayısıyla modeli
yaparken ölçüleri %1 büyük yapmamız gerekir.
Bazı
metallerin çekme miktarları:
DÖKÜM
GERECİ |
ÇEKME
(%) |
OLABİLECEK SAPMA DEĞERİ |
Dökme
demirler:
Lamel
grafitli
Küresel grafitli Tavlanmamış
Küresel grafitli tavlanmış |
1.0
1.2
0.5 |
0.5...0.3
0.8...2
0.0...0.8 |
Çelik
döküm
Sert mangan çeliği |
2.0
2.3 |
1.5...25
2.3...2.8 |
Temper
döküm:
Beyaz
temper döküm (GTW)
Siyah temper döküm (GTS) |
1.6
0.5 |
1.0...2
0.0...15 |
Alüminyum döküm alaşımları |
1.2 |
1.0...1.5 |
Magnezyum döküm alaşımları |
1.2 |
1.0...1.5 |
Bakır
dökümler (Eloktrolit)
Bakır kalay alaşımı (Bronz)
Bakır Çinko alaşımı (Pirinç)
Bakır çinko kalay alaşımı (Kızıl döküm) |
1.9
1.5
1.2
1.3 |
1.5...2.1
0.8...2.0
0.8...1.8
0.8...1.6 |
Özel
Pirinç Döküm (Cu-Zn-Mn-Fe-Al) |
2.0 |
1.8...2.3 |
Çok
gereçli alüminyum bronzu
Çinko döküm alaşımları |
2.1
1.3 |
1.9...2.3
1.1...1.5 |
Beyaz
metal (kurşun-kalay) |
0.5 |
0.4...0.6 |
Çekmeye etki eden faktörler:
a) Parçanın şekli: İnce ve düz parçalar en büyük değerde
çekmelerle karşı karşıyadır, girintili çıkıntılı ve karışık
şekilli parçalarda çekme daha az olur.
b) Parçanın kalınlıkları: Kalın bir parçadaki çekme ince parçaya
göre daha az olur; fakat iç boşluklar veya ince kesitlerde
çatlamalar görülebilir. Bunlar besleyici koymak veya model
konstrüksüyonunda kesit düzenlemeleri ile ortadan
kaldırılabilir.
c) Kalıbın şekli: Maçalı kalıplarda çekme daha az oranda
görülebilir.
3-Yolluk ve besleyiciler: Potanın ağzından dökülen ergiyik
madenin kalıp boşluğuna dolmasını sağlayan yola yolluk denir.
Yolluk sistemi beş parçadan meydana gelir.
1-Dik yolluk: Potadan dökülen madenin sakin olarak curufluk ve
memelere akıtılması için kullanılır.
2- Diplik: Madenin kalıp dibinden kum koparmasını ve turbulansı
önlemek amacıyla kullanılır.
3- Memeler: Madenin kalıba veya besleyiciye aktarılmasını
sağlar.
4- Curufluk: Madenin curuflarının tutulduğu boşluklara curufluk
denir.
5- Besleyici:Kalıptaki kalın kesitleri önlemek amacıyla
kullanılır.
Yolluk sisteminin
özellikleri:
1- Sistem maden ile gelen ve madenin dağılımı sırasında ortaya
çıkan curuf, tortu, kalıp kumu vs. tutacak ve kalıba bunlardan
arınmış temiz madenin girmesini sağlayacak önlemleri
içermelidir.
2- Sistem döküm verimini artırmalı ve sıcaklık dağılımı
yaratmalıdır.
3- Yolluk sistemi kalıplanması kolay ve ağırlık açısından
ekonomik olmalıdır.
4- Sıvı maden akışı sakin, sabit debili ve en alt seviyede
türbülanslı olmalıdır böylece kalıp gazlarının sıvı madende
emilmesi, madenin oksitlenmesi ve kalıbın erozyonu önlenmiş
olur.
5-Sıvı maden kalıp boşluğuna katılaşmaya başlamadan dolmalıdır.
4-İşleme Payları:
a- Tanımı:İşleme yüzeyi ve işleme payı imalat resmi üzerinde
belirtilen işaret o yüzeyin dökümden çıktığı gibi değil dökümden
sonra özel bir işlemeye tabi olacağını gösterir. Bu yüzeylere
işleme yüzeyleri denir.
İşleme payı: İşlenecek yüzeylere yüzey ölçülerine ve kalitesine
bağlı olarak modele verilen fazlalığa işleme payı denir.
Dökme demirler için standard işleme payları:
|
300 e
kadar |
300-600
arası |
600-1000
arası |
1000-1500
arası |
1500-2000
arası |
2000-3000
arası |
|
Dış
kısım |
Silindirik |
|
|
İç
kısım |
|
2.5
3 |
3
5 |
5
7 |
6
8 |
8
10 |
10
12 |
|
Üst
kısım |
Uzunluk |
Yan
Kısım |
|
Alt
Kısım |
|
4~5
3~5
2.5~5 |
5~7
6~7
4~5 |
7~10
6~7
5~6 |
10~12
7~9
6~7 |
12~15
9~11
7~9 |
15~20
11~15
9~12 |
Dökme
Çelikler standard tesviye payları
MAX.
UZUNLUK
(mm) |
EN
AZ (mm) |
ORTALAMA (mm) |
Alt
kısım |
Yan
kısım |
Üst
kısım |
Alt
kısım |
Yan
kısım |
Üst
kısım |
100
mm.ye kadar
100-200
200-400
400-800
800-1600
1600-3150
3150-6300 |
3
3.5
5
7
9
12
15 |
4
4.5
6
8
11
14
17 |
6
6.5
8
10
13
16
19 |
4
4.5
6
8
11
13
16 |
5
5.5
7
9
12
15
18 |
7
8
10
12
16
20
25 |
İşleme
kolaylıkları: İşlemeyi kolaylaştırmak için alınan önlemlerin
amacı:
1- İşin tezgaha bağlanmasını kolaylaştırmak
a) iki punta arasında tur edecek silindirik parçaların eğik
kısımlarına tezgaha bağlanabilmeleri ve punta havşaları
açılabilmesi için çıkıntı parçalar eklenir.
b) Üçgen veya küresel biçimli parçaların tezgaha
bağlanabilmeleri için ayaklar veya kulaklar eklenmelidir.
2- Bazı işlemlerin devamını sağlamak (delme, raybalama ve diş
açma gibi)
3- Tezgaha bağlanması güç ve pahalıya mal olacak işlerin
bağlanmasını kolaylaştırmak amacıyla işlenecek yüzeyleri bir
araya toplamak.
4- Küçük parçaların dökülmesini ve işlenmesini kolaylaştırmak
için sonradan ayırma işlemini uygulamak üzere bir araya
getirmektir.
İşleme payına etki
eden faktörler:
1- Dökülecek malzemenin cinsi: Dökülecek malzeme dökme demir
veya çelik ise yaş kalıplara dökümü sonucunda yüzey sert olur.
Yüzeyin sert tabakasının altından işleme yapmak gerekeceğinden
en az 3 mm.işleme payı vermek gerekir.
2- İşlenecek yüzeylerin büyüklüğü: İşlenecek yüzeyler el
takımları ile işlenecekse yüzeylere 2 mm. İşleme vermek
yeterli olabilir büyük yüzeyler işlenecekse bu yüzeyin
dökümden sonra deforme olacağı dikkate alınarak 8~12 mm işleme
payı verilebilir.
3- Makine veya elde yapılması: El takımı ile işlenecek
yüzeylere işleme payı az verilir; makinede işlenecek yüzeylere
yüzeyin işlenme hassasiyeti göz önüne alınarak 3 mm. Veya daha
fazla işleme payı verilebilir.
Döküm gereç
sembolleri:
GG, GGL- TS:DDL (DIN 1691) Lamel grafitli dökme demir:
Genellikle makine gövdelerinin yapımında kullanılır, ağır yük
çekme ve basmaya karşı mukavimdir fakat ani darbelere karşı
kırılgandır.
GGG-DDK- TS:DDK (DIN 1693) Küresel grafitli dökme denir: Ani
darbelere karşı mukavimdir, esnektir ve kırılganlık özelliği
azdır tavlanmış ve tavlanmamış olarak kullanılır.
Dökme çelik: Ergime derecesi 1450 derecedir, modelcilikte seri
kalıplanan maça sandıklarının yapımında, vakum modellerinin
yapımında, kokil döküm kalıplarının yapımında ve kopya
modellerinde kullanılır.
Takalama: Modellerin kum
kalıp içerisinden çıkarılabilmeleri amacıyla yapılan işlemdir.
Modele bağlanan takalama demirine takılan takalama çubuğuna
çeşitli yönlerden vurularak kalıp boşluğu genişletilebilir.
-Aşırı takalama kalıpta ölçü değişikliğine yol açacağı için
tercih edilmez.
Az takalamada ise model sıkışık olacağı için çıkarılırken kum
kalıbı kırabilir ve kalıp bozulabilir.
MAÇALI MODELLERDE
STANDARD ALT VE ÜSTMAÇA BAŞI ÖLÇÜLERİ
ÜST
MAÇA BAŞI |
ALT
MAÇA BAŞI |
D |
D2 |
H |
D |
D2 |
H |
25 |
22 |
20 |
25 |
24 |
30 |
30 |
27 |
25 |
30 |
29 |
35 |
35 |
32 |
25 |
35 |
34 |
40 |
40 |
37 |
25 |
40 |
39 |
45 |
45 |
42 |
30 |
45 |
44 |
50 |
50 |
47 |
30 |
50 |
49 |
50 |
55 |
52 |
35 |
55 |
54 |
55 |
60 |
57 |
35 |
60 |
59 |
60 |
65 |
62 |
40 |
65 |
64 |
60 |
70 |
67 |
40 |
70 |
69 |
60 |
75 |
72 |
40 |
75 |
74 |
60 |
80 |
77 |
40 |
80 |
79 |
60 |