Kuru kum
kalıplar, yaş kum kalıplara benzer şekilde hazırlanır ve 15-350˚C
arasındaki sıcaklıklarda kurutulurlar. Bağlayıcı görevi yapan
kilin tüm suyunu kaybetmemesi için 400˚C sıcaklığın üzerine
çıkılmamalıdır. Zira tüm suyun kaybolması kumların mukavemeti
üzerinde yıkıcı bir etki yapar.
Kurutma
öncesinde metalin döküleceği kalıp boşluğunun yüzeylerine uygun
bir karışım sürülerek veya püskürtülerek bu bölgede daha yüksek
sertlik ve refrakterlik elde edilebilir.
Kurutmada
kaybedilen zaman başlıca dezavantajı teşkil eder. Kalıp boşluğu
yüzeyinin 2-2,5 cm. Derinliğine kadar kurutulması ile hazırlanan
“kabuğu kurutulmuş” kalıplar, kuru kum kalıp yönteminin bir başka
türü olmaktadır.
Kuru kum
kalıplarda serbest nem buharı olmadığından kalıp havalandırması
problemi çok azalmaktadır. Daha düşük geçirgenlikli kumların
kullanılabilmesi, bu yöntemle daha iyi döküm yüzeyi elde etmek
imkanı sağlar. Yaş kum kalıp yöntemine nazaran, nem kontrolü daha
az kritiktir. Ayrıca kalıbın dökümünden önce bir müddet beklemesi,
yaş kum kalıplarda olduğu gibi kuruma ve yüzeyin gevrekleşmesi
gibi sorunlara yol açmaz.
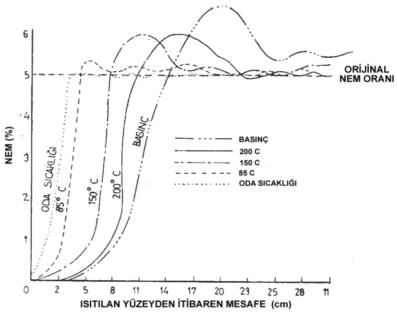
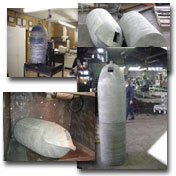
Şekil SEQ
Şekil \* ARABIC 1 Kurutma sıcaklığının nem dağılımına etkisi
Yüzey
kurutmada, ısıtma esnasında buharlaşan nem, kum içinde her yöne
yayınabileceğinden, kurutma kendi kendine havada değil fakat bir
ısı kaynağı ile yapıldığında, sıcaklık artışına paralel olarak
önemli oranda bölgesel nem konsantrasyonu meydana gelebilir. Bunun
nedeni, ısıtılan yüzeyden uzak, soğuk bölgedeki kondensasyon
olayıdır. Bu davranış şekildeki (bkz. Şekil 1) eğride açıkça
görülebilir.
Oda
sıcaklığında nem yalnız kurutulan yüzeyden dışarı çıkar, oysa daha
yüksek sıcaklıklarda nemin hareketi ker iki yönde olmakta ve
kondensasyon bölgeleri meydana gelmektedir. Bu bölgelerde nem
oranının, orjinal değerinin %60 üzerinde bir değere ulaşabildiği
gösterilmiştir. Dalayısı ile bu tür kısmen kurutulmuş kalıplarda,
vakit kaybetmeden döküme geçmek gereklidir.
Yüzey kurutma
işlemi hamlaçlar, ısıtıcı lambalar veya elektrikli ısıtıcı
elemanlarla yapılabilir. Havadan tekrar nem kapmak ki, bu yalnız
havadan değil, kurutulmamış kısımlardan gelen nem’i de içerir,
kurutma işleminden sonraki ilk 24 saat içinde yaklaşık olarak
%0,5-0,8 oranlarında nem olacak şekilde meydana gelir. Nemdeki bu
yükseliş mukavemette bir azalmaya neden olmakla beraber çok kısa
süreli bir ısıtmayla giderilebilir.
Özetlemek
gerekirse:
Kalıplama
yöntemi |
Parça
ağırlığı
(kg) |
En az cidar
kalınlığı (mm) |
Yüzey
pürüzlülüğü
(μm) |
Boyu
hassasiyeti
(mm/m) |
Çekme
dayanımı (mpa) |
Üretim hızı
(parça/saat) |
Gözeneklilik |
Hurda
miktarı |
Kuru kum |
>0,1 |
3,4 |
6,25 |
30-60 |
130 |
1-300 |
5 |
5 |
3-1:en az
5:en çok
Tablo SEQ
Tablo \* ARABIC 1 Kuru kum kalıplama yönteminin bir takım
özellikleri
Kuru kum
kalıplara
döküm yönteminin başlıca üstünlükleri:
·
Dayanımı ve metal erezyonuna karşı dayanıklılığı vakumdan daha
yüksektir.
·
Taşınırken bozulma tehlikesi daha azdır.
·
Yaş kum kalıplardaki gibi kalıplama sırasında nem miktarının
kontrolü kritik değildir.
·
Döküm sırasında buhar oluşmayacağından, bu nedenle ortaya çıkan
döküm kusurları söz konusu değildir.
·
Gaz geçirgenliği daha iyidir.
·
Kalıp havalandırması problemi çok azdır.
·
Daha düşük geçirgenlikli kumların kullanılabilmesi sayesinde daha
az yüzey pürüzlülüğü sağlanabilir.
Yöntemin
sakıncası ise kurutma işleminin kalıp hazırlama süresini uzatması
ve maliyeti arttırmasıdır.
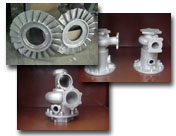
|