ÇELİK ÖZELLİKLERİ VE ÇELİK SEÇİMİ
Çelik seçimindeki temel etmenlerin başında çelik
özellikleri gelir. Çelik seçimi, uygulamanın gerektirdiği özellik
değerlerim karşılayacak en uygun çeliği bulma işidir. Çelik
seçimi özelliklere bağımlı olduğundan tasarımda mühendisin öncelikle
yapması gereken, tasarımım yaptığı parçanın çelik seçimi için,
uygulamanın gereksinimlerim belirlemektir. Bunlar belirlendikten
sonra, aranan çeliklerin özellikleri ile diğer etmenler
karşılaştırılarak en uygun çelik seçilmeye çalışılır,
Çelik özellikleri bu denli önemli olduğundan
özelliklerin tanımlanması ve kısaca anlatımlarıda yarar vardır.
Her bir özelliğin ayrıntıları ve uygulama örnekleri ileriki bölümlerde
verilecektir. Bu nedenle bu bölümde, sık sık sözü edilen "özellikler"
anlam bakımından tanımlanacak ve içyapısal açıdan vurgulanarak
tanıtılmaya çalışılacaktır.
Çelik özellikleri gerçekte tüm gereçler(malzemeler)
için geçerli olan özelliklerdir. Bölümün başlığına çelik özellikleri
denilmesinin nedeni, konunun çelik seçimi olmasındandır.
Çelik seçiminde göz önüne alınan özellikler 6 bölümde
incelenebilir.
1. Kimyasal özellikler
2. Fiziksel özellikler
3. Metalbilimsel özellikler
4. Mekanik özellikler
5. Boyutsal özellikler
6. Yapısal özellikler
2.1. Kimyasal Özellikler
2.1.1. Bazı Kavram ve Tanımlar
Kimyasal özelliklerin tümü çeliğin kimyasal bileşimi
temel alınarak incelenir. Çeliğin kimyasal bileşimi, çeliği oluşturan
elementlerin oransal değerlerinin tümüdür. Her bir elementin çeliğin
özelliklerini belli yönde azaltma ya da artırma eğilimi vardır. Bir
çeliğin özelliklerini incelerken, bileşimindeki elementleri teker
teker ele alıp her birinin etkisini belirlemek gerekir, örneğin,
karbon, sertlik ve çekme dayancını(dayanım veya mukavemet);
mangan ve nikel, tokluğu; bor sertleşebilirliği; krom, ısı ve
yenim(aşınma) direncim; molibden, vanadyum ve volfram kızıl
sertliği ve aşınma direncim artırmada en etkin elementlerdir.
Alaşım elementi deyimi, çeliğin özelliklerini belirli
yönde etkilemek amacıyla çelik bileşimine bilinçli ve ölçülü olarak
alaşım katımları yapıldığında kullanılır. Hurda ya da katkı
maddelerinden rastlantısal olarak çelik bileşimine girmiş olan
elementler alaşım elementi olarak değerlendirilmemelidir.
Alaşımlı çelik, bileşiminde alaşım elementi bulunan
çeliktir.
Katışkı (=empürite) deyimi, çeliğin bileşimine çelik
üretiminde kullanılan hammadde ile katkı maddelerinden rastlantısal
olarak girip üretim sırasında giderilememiş olan elementler için
kullanılır, ilim çeliklerde fosfor, kükürt, bakır, çinko, kalay,
kurşun, arsenik v.b. elementler katışkı olarak bulunur. Buna karşın,
bu elementlerin Şürli bir özelliği geliştirmek için bilinçli ve ölçülü
katımları söz konuşu olduğunda, bunları "katışkı" olarak de-§'1,
alaşım elementi olarak tanımlamak gerekir. Buna belirgin bir örnek,
kolay işlenebilir çeliklerden (= otomat Çelikleri) verilebilir.
Bu çeliklerin talaşlı işlemelerinin kolay ve hızlı
yapılabilmesi için bileşimlerine kükürt, fosfor, kurşun, teluryum ya
da bizmut ya ayrı ayrı ya da birlikte katılır. Bu durumda bu
elementler, katışkı olarak değil alaşım elementi olarak
değerlendirilmek durumundadır, örneğin, çoğu çeliklerde kükürt en çok
% 0.050 S düzeyinin altında olsun istenir. Bu durumda kükürt çelik
içinde bir katışkıdır. Halbuki kolay işlenir (= otomat) çeliklerin
bazılarında kükürt, çelik bileşimine % 0.35 S oranına dek bilinçli
olarak katılmaktadır.
Benzer biçimde bakırdan da söz edilebilir ^Genellikle,
yapı çeliklerinde bakırın en çok % 0.2 Cu düzeyini geçmesi istenmez,
özellikle sıcak işlem görecek çeliklerde yüksek oranda bakır bulunması
onlarda, sıcak gevreklik adı verilen ve yüksek sıcaklıklarda işlem
görürken çatlama ve yarılma biçiminde ortaya çıkan bir olgu doğurur.
Halbuki, atmosfer yenimine karşı direnci artırmak için açıkta
kullanılacak boru çeliklerinin bazılarına % 0.5 -l ,0 Cu oranlarında
bakır katılabilmektedir, tik örnekte katışkı durumunda olan bakır,
ikinci örnekte alaşım elementi olarak iş görmektedir.
Hidrojen, çelik üretiminin çeşitli aşamalarında yapılan
kimyasal çözümlemelerde genellikle aranmayan, bakılmayan bir
elementtir. Fakat çelik yapısında birkaç ppm düzeyinin üzerinde
bulunursa, oluşturacağı hi
gazı kabarcıkları kılcal çatlaklara yol açarak çeliğin
gevrekliğim artırır. Hidrojen gevrekliği diye bilinen bu olgu,
uygulamada çok tehlikeli sonuçlar yaratabilir. Çelik üretiminde
nemli, yağlı, gresli, boyalı v.b, hidrokarbonlu hammadde ile katkı
maddeleri kullanımından kaynaklanan hidrojen, çelik içindeki en
tehlikeli katışkılardan biridir.
Kalıntılar, çelik üretimi sırasında oksijen üfleme ve
oksijen giderme (=deoksidasyon) işlemleri ile daha sonraki döküm
işlemi sırasında oksijen kapma sonucu sıvı çelik içinde oluşmuş ve
yapıda kalmış olan kimyasal bileşiklerdir. Bunlar oksitler,
sülfürler, oksi-sülfürler, alüminatlar ve. silikatlar gibi değişik ve
karmaşık bileşikler olabilir. Herbir türü aynı etki göstermelerine
karşın, bir genelleme ile değerlendirilecek olurlarsa, çeliğin mekanik
özelliklerini etkiledikleri ve en çok da enine çarpma direnci ile
yorulma direncim bozdukları söylenebilir.
Bu özelliklerin yüksek istendiği uygulamalarda, seçilen
çeliğin içyapısı içinde kalıntıların olabildiğince düşük düzeylerde
olması gerekir. Bunu sağlamak için bir yandan çelik üretiminde özel
yöntemler uygulanmağı zorunludur; diğer yandan da çelik kullanıcısı,
üreticinin sağladığı çeliğin bu özellikleri tutup tutmadığım
saptayacak deneyleri yapmaya hazır olmalıdır.
Çeliğin yapısından kaynaklanan kırılmaların çok büyük
çoğunluğu, pis çeliklerde görülür. Pis çelik ile temiz çelik ayrımı
son 20 yıl içinde ortaya çıkmış ve çelik içyapısının katışkı ve
kalıntılardan arındırılmışlığının bir ölçüşü olarak kullanılmaya
başlanmıştır.
Temiz çelikler, yapılarında katışkı ve kalıntıların en
az oranlarda bulunduğu çeliklerdir. Uçak, roket, uydu gibi araçlarda
kullanılan çeliklerin, beklenmeyen facialara yol açmamak için, temiz
çelik olarak özenle seçilmeleri ve üretilmeleri zorunludur.
Temiz çeliklerin üretimleri, temelde, oksit ve
sülfürlerden oluşan kalıntıları en az düzeye indirecek yöntemleri
içerir. Vakum altında eritme, vakum altında gaz giderme (=degazlama),
dışık (= cüruf) altında eritme v.b. yöntemler temiz çelik üretiminde
uygulanan yöntemlerin bazılarıdır.
Çeliğin pislik ya da temizlik kertesi, onun
içyapısındaki kalıntıların incelenmesi ile belirlenebilir. Kalıntıları
belirleme ya metalografi yöntemleri* ya da bozumsuz inceleme
(=tahribatsız muayene) yöntemleri kullanılarak yapılır. Çeliği
üretenler kadar kullananların da bu konuda titizlikle davranmaları ve
şartnamelerin bu konuyu içermelerini sağlamaları gereklidir.
içyapı (== mikroyapı), çeliğin mikroskop altında
50X'den çok büyütmelerde görülen yapışma verilen addır. Çıplak gözle
ya da 10X büyütmeye dek gözlemlenen yapıya ise kabayapı adı verilir,
içyapı incelemeleri, bize tane sınırları, tane büyüklüğü, çelik
yapışım oluşturan evreler (= fazlar) gibi çeliğin içyapısının
bileşenleri hakkında bildi verebilir.
İçyapı, çeliğin kimyasal bileşimine bağımlıdır. Bu
bağımlılık bazı durumlarda doğrudan bazı durumlarda ise dolaylı olur.
Örneğin, mangan ve nikel çeliğin yapışım ostenitli bir yapıya
dönüştürerek doğrudan etkin olabilirler; Al, V, Ti ise azot ile nitrür
bileşiklerim oluşturarak tane büyümesini engelleyip dolaylı olarak
küçük taneli yapı oluştururlar. Çeliklerin dayancını artırmada çok
etkin olan tane küçültme böylece kimyasal bileşime Al, V, T
katımlarıyla sağlanabilir. Ayrıca, çeliğin dayancını artırma
yöntemlerinden bir diğeri de, içyapısında ince taneli ve eşdağılımlı
olarak karbür çökelimine dayanır. Karbür yapıcı olarak bilinen ve
çeliklerin bileşimine giren teme metaller krom, vanadyum, molibden ve
volframdır.
Çeliğin en önemli özelliklerinden biri olan
sertleşebilirlik de kimyasal bileşim ayarlaması ile sağlanır : Alaşım
elementlerinin en etkinleri bor, krom ve molibden metalleridir.
Görüldüğü gibi, içyapı ile kimyasal bileşim karşılıklı
etkileşim içindedir. Bu nedenle, içyapılar hem çeliklerin
özelliklerini yaratan temel nedenlerin belirlenmesi ve hem de
çeliklerin yapılarından kaynaklanan sorunların çözümlenmesi bakımından
çok önemlidirler. Kimyasal bileşim ile çeliğin içyapısı, içyapı ile de
özellikler arasındı varolan bağıntılar, çelik üretiminde denetimi ve
ayan daha kolay yapılabilen kimyasal bileşim yoluyla çelikte istenilen
özelliklerin yaratılmasını sağlar.
Alaşım elementleri, çeliğin ferrit ya da ostenit
evresini daha dengeli kılmalarına bağlı olarak ferrit oluşturucular ve
ostenit oluşturucular diye adlandırılır.
Mangan ve nikel ostenit oluşturucu elementlerdir; krom,
vanadyum, molibden, volfram elementleri ise karbür yapıcılıklarının
yanısıra ferrit oluşturucu olarak da bilinirler.
Birikim olgusu alaşım elementleri, katışkı ve
kalıntıların tane sınırı, dallantı (=dendrit) sınırı v.b. yerlerde
katılaşma ya da ısıl işlem sırasında, kimyasal bileşimin ortalama
değerlerinden sapacak düzeylerde, toplanmalarıyla ortaya çıkar.
Birikim sonucu oluşan nesne topluluğuna birikinti adı verilir. Çelik
yapışı içinde fosfor birikintiler, sülfür birikintileri v.b. katışkı
birikintileri olabildiği gibi, alaşım elementlerinin ve kalıntıların
da birikintileri olabilir. Çelik yapışı içinde birikintilerin
bulunması hem içyapının eşdağılımlılığını ve hem de özelliklerin
eşyönlülüğünü (==izotropi) bozar. Bu nedenle, kimyasal bileşim,
katılaşma koşullan ve ısıl işlem koşullarıyla birlikte çeliklerin
özelliklerin i bu yönden de etkiler.
Yenim (= korozyon) olgusu : Yenim direnci, çeliğin
içinde bulunduğu ortamda kimyasal ya da elektrokimyasal etkileşim
sonucu bozulmaya karşı gösterdiği direnmedir. Yenim direnci,
Özellikle, kimyasal ya da elektrokimyasal etkileşimin yüksek olduğu
yenimli ortamlar içinde çalışan parçalar için çok önemlidir.
Yenim olgusu birçok biçimde oluşur. Çoğu mühendis
"yenim" deyince yalnızca çeliğin paslanmasından söz edildiğim sanır.
Pas, belli tür bir yenimin yan ürünüdür. Yenimin türü ne olursa olsun,
bu olgunun sonunda çelikte bir bozulma olur. Bu bozulma, bazı
durumlarda ağırlık azalması; bazılarında ağırlık artması ve diğer
bazılarında ise mekanik özelliklerde bozulma biçiminde gelişir.
Yenim olgusunun yalnızca sıvı ya da gaz kimyasal
ortamlarda oluştuğu düşünülmemelidir. Olağan oda atmosferinde de çoğu
çelikler paslanabilir. Bu nedenle, yenim, bir çelik parçanın ya da
makinanın çalışmasını engelleyebilecekse yenim direnci çelik seçiminde
en önemli etmen durumuna gelebilir.
Paslanmaz çelikler bu kitabın kapsamı dışında
bırakıldığından yenim konuşu incelenmeyecektir.
2.2. Fiziksel Özellikler
Çelik uygulamalarında geçerliliği olan fiziksel
Özellikler doğrudan uygulama gereklerine bağlı olarak önem kazadır.
Fiziksel özellikler, genelde, ısıl özellikler, elektriksel özellikler,
mıknatıs Özellikler ve yoğunluksal özellikler olarak alt bölümlere
ayrılırlar. Bunlar üzerinde durmayacak, yalnızca kısaca bir iki
noktaya değineceğiz.
Isının önemli bir değişken olduğu uygulamalarda,
çeliğin türüne bağlı olarak, ısıl iletkenliğinin bilinmesi ve
tasarımda göz önüne alınması gereklidir. Bununla ilişkili ikinci bir
önemli özellik ısıl genleşmedir. Alüminyum gibi çeliğin iki katı
genleşen bir metal, çelik ile birlikte kullanılacaksa tasarımcı
mühendisin bunu, tasarımında çok iyi değerlendirmesi gerekir.
Elektrik ve mıknatıs özellikler trafo sacı gibi
uygulamalar için yapılan çelik seçimlerinde önem kazanır.
Fiziksel özellikler çelik seçiminde çok özel
uygulamalar için önem kazanırlar. Genellikle, en önce değerlendirilen
özellikler değillerdir.
2.3. Mekanik Özellikler
Çelik seçiminde öncelikle ve de en çok değerlendirmeye
giren özellikler mekanik özelliklerdir. Şüphesiz, hiçbir uygulamada bu
etmen tek ve yalnız basma kullanılmamalıdır. Bununla birlikte
tasarımda ilk düşünülüp değerlendirilen bu etmendir.
Tasarım işinde kullanılan çeliklerin dayanç ve süneklik
değerleri çekme deneyinden elde edilir. Çeliklerin uygulamadaki
davranımlarını, çekme deneyinden elde edilen bu tür özellik
değerlerinden kestirmek olasıdır. Makina ya da yapı tasarımında
kullanılan bir parçanın çekme deneyinden elde edilmiş dayanç ve
süneklik ya da uzama değerleri, gerçek uygulama koşullarında
karşılaşılan yük ve süneklik değerlerine çok yakın bulunur. Bu
nedenle, tüm çelik tasarımlarında çeliklerin sünek davranımı çelik
tasarımının olağan ve doğal bir yanı gibi görülür. Fakat, aşağıda da
değineceğimiz gibi, bazı yükleme koşulları altında çelikler gevrek
davranım da gösterip beklenmedik kırılmalara yol açabilirler, işte bu
davranım biçimlerine ışık tutan en yaygın ve belki de en yararlı deney
çekme deneyidir.
2.3.1. Çekme Özellikleri
Çekme deneyleri Şekil II.l'de basitçe gösterilen
çekme aygıtında standart deney çubuktan kullanılarak yapılır.
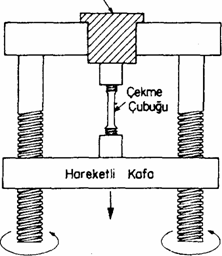
Çekme Deneyi Aygıtı
Bu aygıtlarla, ayarlanabilen uygulama hızları ve
yükleri kullanılarak, ister çekme deneyi ister basma deneyi
yapılabilir. Çekme deneyleri aşağıda sıralanan çekme deneyi
standartlarına uygun olarak yapılmalıdır :
İSO / 82 - 1974
DİN 50 145 - 1975
ASTM A 370
SAE J 416 b
BS 18 Fart 2-1971
NF A 03-151-1971
JIS Z 2001 - 1968
TSE 138
Uluslararası standartlarda çekme deneyine ilişkin
olarak Çizelge II-l'de verilen simgeler ve birimler
kullanılmaktadır.
Çekme deneyi uygulamasında bir yandan uygulanan yük ve
diğer yandan standart deney çubuğunun uzaması belirlenip, Şekil
n.2a'da görüldüğü gibi bir yük-uzama eğrisi çıkarılır. Bu eğriden
daha belirtgen olarak kullanılan gerilim-gerinin eğrisi de
çizilebilir (Şekil II.2b).
(a)
(b)
Şekil II. 2a) Yük-Uzama
Eğrisi Şekil II. 2b
Gerilim -Gerinim Eğrisi
Anılan eğrilerden yararlanarak bazı tanımlamalar
yapalım: Gerilim, birim alana düşen yüktür :
= F/S (N/mm2)
Gerinim, birim boya düşen uzama, ya da kısaca, uzama
oranıdır:

Esnek bölge, çeliğin, uygulanan yük kalktıktan sonra
tümüyle ilk boyutlarına dönebildiği esnek davranım bölgesidir.
Yoğruk bölge, çeliğin yoğruk bozunuma (= plastik
deformasyon) uğrayıp kalıcı uzama, ya da daha başka bir deyişle, biçim
değişikliği gösterdiği davranım bölgesidir.
Orantısal kısıt, esnek davranımdan yoğruk davranıma
geçilen gerilim değerine verilen addır. Esnek bölgede gerilim,
gerinimle doğru orantılıdır. Bu orantı katsayısı, esneklik katsayısı
(= elastik modülü) yada Young katsayısı ve bu kural da Hooke Yasası
diye bilinir. Orantısal kısıt, Hooke Yasası'nın uygulanma kısıtlarını
belirtir. Esneklik katsayısı, çeliğin esnemezlik ya da bükülmezlik
özelliğinin bir ölçüsüdür. Yük altındaki esneme miktarını belirttiği
için tasarımda çok önemlidir.
Akma gerilimi; düşük karbonlu çelikler esnek
davranımdan yoğruk davranıma geçerken gerilimin artmamasına karşın
gerinimin arttığı çok belirgin ve farklı bir davranım gösterirler. Bu
olaya akma, akmayı sağlayan gerilime de akma gerilimi denir. Belirgin
bir akma geriliminin olmadığı durumlarda akma dayancından söz edilir.
Her çelik belirgin bir akma göstermez. Bu gibi
durumlarda önceden saptanmış bir gerinimi (% 0.2, % 0.5 gibi) sağlayan
gerilim değerleri kullanılır. Bu nedenle de akma gerilimi yerine % 0.2
akma gerilimi, % 0.2 öteleme gerilimi gibi deyimler kullanılır.
Düşük ve orta karbonlu çeliklerde gerilim-gerinim
eğrisi. Şekil III.3'te gösterildiği gibi bir üst akma noktası
ve bir de alt akma noktasından geçer. Bu davranım, yoğruk bozunumun
içyapı içinde eşdağılımlı olmamasından kaynaklanır ve gerilim
yoğunluğunun yüksek olduğu noktalarda başlar. Yoğruk bozunumun böylece
aşamalı olarak gelişmesi yüzeyde gözle görülebilir çizgiler biçimine
dönüşür. Bunlar Lüder çizgileri diye anılır.
Şekil
Düşük ve Orta Karbonlu Çeliklerde Akma
Davranımı
Yukarıda anılan eğrilerde kullanılan gerilim, uygulama
yükünün (F0) ilk kesit alanına (S0) oranı
alınarak bulunur. Gerinim, Є ise deney çubuğunun belirlenmiş bir ilk
uzunluğundaki değişimin,
(L),
ilk uzunluğa (L0), oranı olarak alınır. Bu
tanımlardan çıkan gerilim ve gerinim mühendislik gerilimi ve
mühendislik gerinimi adlarıyla anılır.
Çekme dayana; en yüksek yükün ilk kesit alanına oranı
olarak tanımlanır :
Rm = (N/mm2) m
Amerikan ve İngiliz standartlarında
kullanılan anglo-sakson birimlerinin metrik birimlere çevrimi
Çizelge 11.2' de verilmiştir. Yoğruk bozunum sırasında hacim
değişikliği olmaz. Bu nedenle, deney çubuğu kesit alanını daraltarak
belverir. Bu bakımdan mühendislik gerilimi ve mühendislik gerinimi
yerine bu kesit alanı değişikliğini de içeren yeni tanımlara gerek
vardır :
Gerçek gerilim, çekme deneyinin herhangi bir anındaki
en küçük kesit alanıyla belirlenen gerilimdir.
Gerçek gerinim ise çekme deneyinin herhangi bir anında
boy uzamasının o andaki boy uzunluğuna oranının türevi olarak
tanımlanır.
La = o andaki boy; L0 = ilk boy
olduğunda gerçek gerinim;
=
ln
olarak verilir. Bu durumda gerçek gerilim - gerçek
gerinim eğrisi Şekil 11.4'de görüldüğü gibi belirlenecektir. Bu
eğri ile mühendislik gerilim - gerinim eğrisi arasında en belirgin
fark yoğruk bölgede görülür: Mühendislik gerilim - gerinim eğrisinde
en yüksek gerilim değerine belverme olgusunun başladığı anda ulaşılır.
Bu gerilim en yüksek çekme gerilimi, ya da yalın olarak, çekme
dayancı adını alır. Halbuki, gerçek gerilim - gerinim eğrisinde
belverme olgusundan ötürü kesit alanı gittikçe daraldığından gerilim,
kopma noktasına dek sürekli artar. Herhangi bir andaki gerçek gerinim
de
=ln
eşitliğiyle verilir. Burada S0= ilk kesit
alanı, Sa= o andaki kesit alanıdır.
GERÇEK ÇERİNİM
Gerçek Gerilim -Gerinim ile Mühendislik Gerilim-Gerinim
Eğrileri Karşılaştırması
Çekme deneyinde, standart çekme çubuğu kopuncaya dek
deney sürdürülür. Kopmuş parça üzerindeki ya da kopma anındaki uzama
oranı ya da belverme olarak beliren kesit alanı küçülmesinin oranı
çeliğin süneklik özelliğinin ölçüşü olarak alınır :
% uzama = x100
L =
uzama farkı; Lo = ilk boy (genellikle 50 mm ya da 100 mm)
% alan küçülmesi=

s =
kesit alanı farkı, S0 = ilk kesit alanı.
Genellikle, % uzama ve % alan küçülmesi ne denli yüksek
olursa, çelik o denli sünektir: kopmaksızın biçimlenebilir. Tek
rakamlı değerlerde kalacak olurlarsa, çeliğin biçimlenebilirlik
özelliği çok düşük olur; soğuk bükme ve derin çekme (= sıvama)
işlemlerinde kullanılamazlar.
Bu işlemler için %30-50 arasında süneklik değerleri
gereklidir. Binalarda, köprülerde, direklerde, borularda, taşıtlarda
ve benzeri birçok durağan (= statik) yük uygulamalarında yalnızca
esnek bozunum söz konusudur; bu nedenle yalnızca akma gerilimini
bilmek tasarım için yeterlidir.
Haddeleme, dövme, sıkma, tel çekme, presleme v.b.
işlemler ise çeliğin çatlama ve kırılmaya varmadan biçim değişimine,
daha doğrusu, yoğruk bozunumuna bağlıdır. Burada çeliğin hem süneklik
özelliği ye hem de çalışma sertleşmesi hızı ya da diğer adıyla
pekleşme hızı önemlidir.
Birçok metallerde pekleşme, yani soğuk yoğruk bozunum
ile yapının sertliğinin ve dayananın artması olgusu, kabaca şu
eksponensiyel eşitliğe uygun olarak gerçekleşir :
T =K.
n
Burada, K = bir değişmez, n = pekleşme üst-katsayısı (<
l),
= gerilim,
= gerinimdir.
İki çelik için n ve K değerleri örnek olarak verilirse
şöyledir:
|
K, N/m2 |
N |
Tavlanmış 1020 |
45 x 107 |
0.30 |
Menevişlenmiş 1060 |
127 x 107 |
0.15 |
Bu denklemle tanımlanan davranımı gösteren metallerde
gerçek gerinim=0 olduğunda, belverme başlar. Gerçek gerilim gerçek
gerinim eğrisinin altında kalan alan,
olarak hesaplanabilir.
Bu alan
= x = kg/cm2
birimiyle, tokluk özelliğünin bir ölçüsü olarak
alınabilir: Bu alan ne denli büyükse tokluk o denli yüksektir.
2.3.2. Basma Özellikleri
Gevrek davranım gösteren gri dökme demir gibi
alaşımların çekme özellikleri zayıftır; yapılarında bulunan kılcal
çatlaklar çekme gerilimleri altında büyüyerek gevrek kırılmaya yol
açar. Bu tür davranımda çekme dayancı genellikle düşüktür; fakat,
yüksek olduğu durumlarda bile çekme dayançları akma dayançlarına çok
yakındır. Bu tür davranım gösteren alaşımlar basma gerilimi altında
çok daha yüksek dayanca sahiptir,
Basma özelliklerini belirlemek için basma deneyi
uygulanır. Bu deney de çekme aygıtına yapılır. Basma gerilimi kesit
alanım artırdığından, basma deneyinde belverme görülmez; şişme vardır.
Basma gerilim - gerinim eğrileri de biçimsel olarak çekme
gerilim-gerinim eğrilerine benzerler.
2.3.3. Kesme Özellikleri
Birçok uygulamada yükleme biçimi kesme yaratır:
Civatalar, perçinler, kamalar, sürgüler v.b., genellikle kesme
gerilimleri altında yarılırlar. Kesme dayancı, kesme gerilimi altında
yarılma ya da kırılmayı başlatan gerilime verilen addır. Şekil II.
5'de gösterilen biçimdeki bir düzenek, çekme aygıtında kesme
deneyi uygulaması için kullanılabilir. Kesme gerilimi değerleri çekme
gerilimi değerleri gibi kolay bulunur çizelgeler durumuna getirilmiş
değildir. Bir ilk yaklaşımla (kesme gerilimi =0.40 x çekme gerilimi)
eşitliğinden çıkarılabilir.
2.3.4. Sertlik Özelliği
Sertlik, çeliğin yoğruk bozunuma gösterdiği dirence
verilen addır. Bunu ölçmek için sertlikölçer aygıtları kullanılır.
Sertliği ölçülecek yüzeye ya sert bir bilya ya da sivri bir uç
uygulanarak çıkarılan izin alanı ya da derinliği ölçülü1'-
Bu değer, çeliğin sertliğinin bir ölçüşü olarak kullanılır.
Aşağıda, çeliklerde en çok kullanılan sertlik ölçüm
yöntemleri ve uygulama alanları özetlenmiştir.
Sertlik Deneyi |
izaçar |
Yük |
Uygulama |
Knoop |
Elmas |
1kg-2000kg |
İncesertlik (mikrosertlik) |
Vickers |
Elmas |
1kg-2000kg |
İncesertlik (mikrosertlik) |
Rockwell C |
Elmas |
150kg |
Kalın ve sert metaller |
Rockwell B |
Çelik bilya |
100kg |
Sertliği yük. olm. çelik ve demirdışı met. |
Rockwell T |
Çelik bilya |
15,30,45kg |
Çok ince ve yumuşak metaller |
Rockwell N |
Elmas |
15,30,45kg |
Sert ve ince metaller |
Brinell |
Çelik bilya |
500-3000kg |
Sertliği 40 HRC’ ye dek çeliklere |
Herbir sertlik ölçme yönteminin kendine özgü
üstünlükleri ve kısıtları vardır. Çizelge 11.3'de de görüldüğü
gibi, değişik sertlik ölçekleri arasında çevrim olasıdır. Fakat bir
ölçekten diğerine geçerken iki önemli husus göz ardı edilmemelidir :
Bunlardan ilki, her sertlik deneyinin en uygun olduğu uygulama alanı
vardır, örneğin, çok ince yumuşak çelik saclara Rockwell B ya da
Rockwell T uygulanabilir; fakat, Rockwell C asla düşünülmemelidir.
ikincisi de, ilkine bağlı olarak, her sertlik ölçeğinin bir geçerlilik
aralığı vardır, örneğin, Rockwell C 20 HRC değerinin altında, Rockwell
B ise 100 HRB değerinin üzerinde geçersiz ve anlamsızdır. Sertlik
değerleri arasında karşılaştırma yapılacağı zaman ayni ölçek değerleri
karşılaştırılmalı, zorunlu olmadıkça çevrim çizelgelerine
başvurulmamalıdır. Mutlak sertlik değerleri incesertlik (=
mikrosertlik) ölçen aygıtlarla ve incesertlik değeri olarak
ölçülmelidir.
Tasarımda istenilen sertlik değerinin ne olduğu ve elde
ediliş yöntemi, ısıl işlem v.b. işlemlere ilişkin olarak
belirtilmelidir. Sertlik değeri tasarım çizimlerinde 35-40 HRC gibi
bir sertlik aralığı ya da en az 50 HRC, en çok 45 HRC gibi kısıtlama
değerleri olarak belirtilir. Tasarımda sertlik değeri ve ölçeğinin
standart belirtme yöntemi şöyledir:
XXX HXX
Burada, ilk üç XXX yerine seçilen ölçekteki sertlik
değeri yazılır. HXX simgesindeki H, İngilizce’deki sertlik (= hardness)
kelimesinin ilk harfini simgeler. H'den sonraki ilk X, sertlik ölçüm
yöntemim belirler ve şu harflerden biri kullanılır :
Knoop için Kx (x = kullanılan yük)
Vickers için Vx (x = kullanılan yük)
Rockwell için R
Brineli için B
HXX simgesindeki son X ise yalnızca Rockwell sertliği
için kullanılır ve Rockwell sertlik deneyinin hangi ölçeği ile geçerli
ise o belirtilir :
Rockwell A için A
“ B “ B
“ C “ C
“ T “ 15T, 30T, ya da 45 T
“ N “ 15N, SON, ya da 45 N
Bu durumda sertlik değerleri tasarımda, şu örneklerde
gösterildiği gibi, belirtilmelidir:
- en çok 56 HRC
- en az 70 HRB
- 380 - 400 HB
- en az 500 HK200 gf
Tasarımda sertlik değerinin ve ölçeğinin doğru
gösterilmesi üretici, yapımcı ve işletmeciyi de yönlendirmiş olur.
Çoğu tasarım uygulamasında çekme dayancının sertlik eşdeğerleri
gerekir. Çizelge 11.4'te N/mm2 birimi türünden
verilen çekme dayancının Vickers, Brinell ve Rockwell sertlik
eşdeğerleri verilmektedir.
2.3.5. Çarpma Özellikleri (= darbe özellikleri)
Çeliklerin çekme, basma, kesme ve burma gibi durağan
yükler altındaki davranımları çarpma gibi devingen yükler altındaki
davranımlarından oldukça farklıdır. Çeliklerin, çarpma davranımlarını
çarpma özellikleri belirler. Çeliklerin çarpma özelliği, çarpma
yükleri altında kırılmaya karşı gösterdikleri dirençtir. Bu özellik
kısaca tokluk diye bilinir.
Çarpma dayancı, çarpma yükü altında çeliğin kırılması
için gereken enerji değeridir; ya joule (J) ya da J/cm3
birimiyle ölçülür.
Çeliklerin çarpma dayançları çarpma aygıtlarıyla
Şekil II. 6a ve Şekil II. 6b'de gösterildiği gibi ölçülür, iki tür
çarpma deneyi vardır : Charpy ve Izod. Bunların her ikisi de belli
ağırlıktaki bir sarkacı belli yükseklikten salarak deney çubuğunu
kırmak için tüketilen enerjiyi bulma temeline dayanır, Izod ve Charpy
deneyleri arasındaki fark. Şekil II.6b'de gösterildiği gibi,
deney çubuğunun duruş biçimine ilişkindir : Charpy deneyinde deney
çubuğu yatay konumda, Izod deneyinde ise dikey konumdadır.
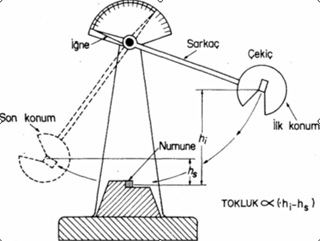
Çarpma Deneyi Aygıtı
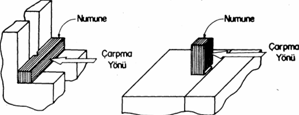
CHARPY
IZOD
Charpy ve izod Çarpma Deneyleri
Şekil II. 7'de
çarpma deneyi için kullanılan standart deney çubukları ölçüleri
verilmiştir. Çubuklar, çentikli kullanılabildikleri gibi, takım
çelikleri türünden çok sert ve gevrek çeliklerde olduğu gibi,çentiksiz
de kullanılabilirler. Çentikli çubuklar kullanıldığında, çarpma
dayancı Charpy V ya da çentikli Izod diye belirtilmelidir. Çarpma
dayancı karşılaştırılmalarında yanlışlıkları önlemek için bu
zorunludur.
Standart Charpy ve Izod deneyleri, çeliklerin gerçek
uygulama koşullarım tam olarak yansıtmamaktadır. Kullanılan deney
çubuğu çok küçük olduğundan büyük ve kalın çelik parçaların
davranımını tam olarak yansıtamazlar. Bu nedenle, son 15-20 yıldır
ağırlık-düşürme deneyi ve devingen yırtma deneyi ile daha gerçekçi
çarpma davranımı belirlemeleri ve kırılma tokluğu kavramı
kullanılmaktadır. Kırılma tokluğuna daha sonra kısa da olsa
değineceğiz. Fakat burada klasik anlamdaki tokluk ve çarpma dayancı
üzerinde duralım :
2.3.5.1. Tokluk Özelliği
Tokluk, çeliklerin çarpma davranımlarını belirleyen
özelliktir. Zor kırılan, yani çarpma dayancı yüksek olan çeliğin
tokluğu yüksek; kolay kırılan, yani çarpma dayancı düşük olan çeliğin
tokluğu ise düşüktür. Çeliğin tokluğu yüksek ise SÜNEK DAVRANIM
gösterir, kolay kırılmaz; tokluğu düşük çelikler ise GEVREK DAVRANIM
gösterir. Davranım biçimlerine bağlı olarak çelikler, suverilmiş
takım çelikleri gibi gevrek, ya da tavlanmış düşük karbonla çelikler
gibi, sünek olarak adlandırılabilirler.
Çarpma deneylerinde, özel durumlar dışında, hep
çentikli deney çubukları kullanıldığından bazı yerlerde "tokluk"
yerine "çentik - tokluğu" deyimi kullanılır. Çarpma deneyi sonuçları
Charpy V ya da çentikli - Izod diye belirtildiği sürece yalın "tokluk"
deyimi bu özelliği anlatmak için yeterlidir. Gerçekte burada en doğru
deyim, çarpma - tokluğu olmalıdır.
Çarpma deneyleri ile belirlenen çarpma-tokluğu,
aslında, çeliklerin içyapıları içinde bulunan kılcal çatlaklar, gevrek
ikincil çökeltiler, tane sınırları v.b, ile yüzeysel kusurlardan doğan
gerilim artırıcı etmenlerin yarattığı çentik duyarlılığı'nı yansıtır.
Ancak, deney çubuklarının küçüklüğünden ve ayrıca, durağan çarpma
özelliğinden ötürü üçlü-eksenel gerilim durumu ve gerilimin
eşdağılımsızlığı söz konusudur. Halbuki devingen yırtma deneylerinde
gerilim, temel olarak, çekme gerilimi özelliğindedir; ayrıca
eşdağılımlıdır. Çarpma deneylerinde çentik dibi çevresinde varolan
gerilim durumu çelik numunenin kalınlığına ve büyüklüğüne göre değişir
ve çeliği deney sonuçlarının belirlediğinden daha gevrek bir davranıma
iter. Değişik büyüklük ve kalınlıklar kullanarak çarpma deneyi
sonuçlarım birleştirmek olası değildir. Bununla birlikte, özellikle,
çeliklerin bileşim, içyapı, ısıl işlem, pekleşme gibi etmenlerinin
çarpma tokluğuna etkilerini göstermek için bu çarpma deneyleri yararlı
olarak kullanılabilir.
Tokluk özelliği üzerine geniş çapta ve ciddi olarak
araştırmalar, II. Dünya Savaşı sırasında Amerikan LIBERTY türü
kaynaklı gemilerin Amerika'dan Avrupa'ya Kuzey Atlantik'te yük
taşırken kış koşullarında ikiye bölünmeleri sonucu başlatılmıştır.
Çok soğuk havalarda ve büyük dalgaların şiddetli çarpmaları sonucu
kaynaklanmış çelik gemiler gevrek davranım göstererek gevrek
kırılmaya uğramışlardır. Olağan olarak sünek olması gereken düşük
karbonlu çelik belirli koşullarda gevrek davranıma geçmektedir, işte
bunu daha iyi anlayabilmek için çarpma deneylerinden
yararlanılmıştır.
Standart çarpma deneyi çubuklar kullanılarak çelikler
üzerinde değişik sıcaklıklarda çarpma deneyleri yapıldığında, çarpma
dayancı ya da tokluk değerinin sıcaklığa karşı çizilen eğrisi Şekil
n. 8'deki gibidir. Bu eğrinin 2 belirgin özelliği hemen görülür :
Çelikler, özellikle yalın karbonlu çelikler ile düşük alaşımlı makina
yapı çelikleri, belirli sıcaklık aralığında sünek davranım
gösterirlerken, düşük sıcaklıklarda gevrek davranım içine
girmektedirler.
Sünek davranım biçiminden gevrek davranım biçimine
geçişi simgeleyen bir geçiş sıcaklığı, Tg, vardır. Sünek davranımdan
gevrek davranıma geçiş, gerçekte tek bir sıcaklık değerinde değil, bir
sıcaklık aralığı içinde olur. Kimi çeliklerde bu sıcaklık aralığı 30°C
gibi geniş ve yaygın, diğer kimilerinde ise 3-5°C gibi çok dar bir
değer aralığında olur. Geçiş sıcaklığı aralığı ne denli dar ise sünek
davranmadan gevrek davranıma geçiş o denli ani ve beklenmedik olur.
Geçiş sıcaklığı kavramı çok yararlı ve yaygın olarak
kullanılmasına karşın, davranımdaki geçiş farklılıklarını tam olarak
yansıtamayabilir. Geçiş sıcaklığının üstündeki sıcaklıklarda çelik
sünek davranım. Altındaki sıcaklıklarda ise gevrek davranım
gösterecektir. Fakat, geçiş sıcaklık aralığı geniş olan çeliklerde bu
geçiş daha yavaş; dar olanlarda ise beklenmedik kırılmalara yol açacak
biçimde birden olur : Kuzey Denizi'nde kış koşullarında kırılan petrol
platformları, ikiye ayrılan gemiler, kışın fırtınada çöken asma
köprüler v.b. bunlara birer örnek olarak verilebilir.
DENEY ÇUBUĞU SICAKLIĞI, oC
Şekil II. 8)
Çarpma Dayancımn Sıcaklığa Bağımlı Olarak Değişimi
Bu denli önemli olan geçiş sıcaklığına daha kesin bir
belirginlik sağlanması amacıyla başka tanımlar da geliştirilmiştir.
Özellikle gemi v.b. yapımında kullanılan düşük karbonlu çelikler için
21J değerine karşı gelen sıcaklık, uygulamada geçiş sıcaklığı olarak
alınır. Bu tanımlamadaki sıcaklık, T21 olarak
gösterilebilir (Şekil II. 9a)
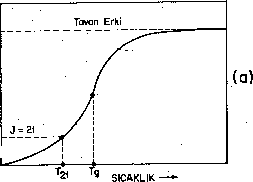
Şekil II 9a)
Geçiş Sıcaklığı tanımları
Daha modern yaklaşımlar kırılma bilimi (= fraktografi)
bulgularından yararlanarak, kırık yüzey görünümlerine dayalı tanımları
içermektedir. Sünek kırılan çeliğin kırık yüzeyinin bu kırılma
biçimini yansıtan donuk ya da mat ve pütürlü, olan belirgin bir
görünümü vardır. Bu görünüm, kesme olgusunu içeren sünek kırılma
biçiminin tanımlaması için kullanılır. Gevrek kırılmış bir çeliğin
kırık yüzeyi, yarılma yüzeylerinden ötürü parlak ve kristalsi
görünümlüdür. Bu bakımdan, kırık yüzeylerin incelenmesi sonucu
deneyimli gözler "gevreklik" ve "süneklik" oranları hakkında bilgi
edinebilir. Bu tür değerlendirmeler sonucu çarpma dayancı - sıcaklık
eğrisine benzer biçimde kırık yüzey görünümü-sıcaklık eğrileri de
çıkarılabilir (Şekil n. 9b). işte, aşağıda belirtilen geçiş
sıcaklıkları böyle yaklaşımlar sonucu tanımlanmıştır :
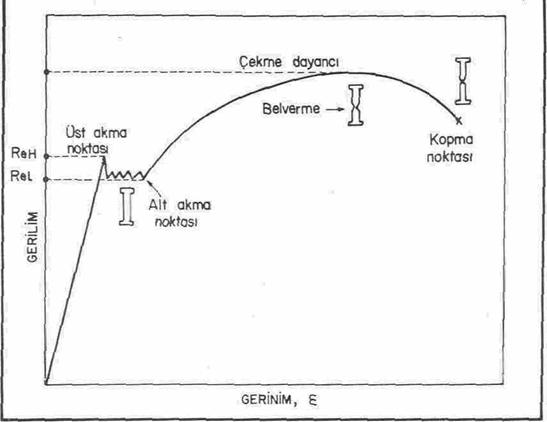
SICAKLIK
Şekil II. 9 b)
Kırık Yüzeyi Görünümünün Sıcaklığa Bağımlı Olarak Değişimi
KGGS, Kırılma Görünümü Geçiş Sıcaklığı İngilizce "fracture
appearance transition temperature" deyiminin kısaltılmışı olan FATT'ın
Türkçe karşılığı olarak kullanılır. Anılan sıcaklık, % 50 gevrek+% 50
sünek kırılmanın görüldüğü sıcaklıktır ve kimi yayınlarda yalnızca
KGGS (=FATT) diye geçmekte ise de % 50 KGGS ya da 50-50 KGGS diye
anılması daha doğrudur.
TGS, Tam Gevreklik Sıcaklığı, İngilizce "nil ductility
temperature" NDT'nin Türkçe karşılığı olarak kullanılabilir ve kırık
yüzeyin % 100 gevrek kırılma gösterdiği ya da diğer bir deyişle kırık
yüzeyde hiç sünek kırılma bölgesi görülmeyen en yüksek sıcaklık diye
tanımlanır. TGS altındaki sıcaklıklarda kırılma % 100 yarılma
biçiminde olur.
Tam gevreklik sıcaklığı, uygulamada T21
sıcaklığına eşdeğer olarak alınabilir; bu sıcaklık, çarpım yükü
altında çalışma olasılığı bulunan uygulamalarda hiçbir zaman 0°C
üstünde olmamalıdır. Tam gevreklik sıcaklığı ne denli düşük değerde
olursa çeliğin tokluğu o denli yüksek olacaktır.
TSS, Tam Süneklik Sıcaklığı, İngilizce "fracture
transition plastic" deyiminin kısaltılmışı olan, FTP karşılığı olarak
verilebilir ve kırık yüzeyin % 100 sünek kırılma biçimi gösterdiği en
düşük sıcaklık ya da, başka bir anlatımla, kendi üzerindeki
sıcaklıklarda gevrek kırılmanın hiç görülmediği sıcaklık diye
tanımlanabilir. TSS üstündeki sıcaklıklardaki kırılmalar daima yoğruk
bozunum içerir ve kırık yüzeylerde kesme olgusunu yansıtan sünek
kırılma gözlemlenir.
Yukarıda değinilen geçiş sıcaklıklarının tümü de
kullanılabilir. Sanayide en çok kullanılanları, geçiş sıcaklığı Tg,
T21, KGSS, ve TGS'dir.
2.3.5.2. Çeliklerde Kırılma Olgusu
Çelik içyapıların kırılma oluş biçimi, çelik seçimi
açısından bilinmesi gereken bir olgudur. Çeliklerin kırılma olguları,
deyine geldiğimiz gibi, iki uç biçimde incelenebilir: Sünek kırılma ve
gevrek kırılma. Tehlike yaratan kırılma, gevrek kırılmadır : Hem
hızlı, hem kolay ve hem de beklenmedik bir anda doğabilir. Eğer,
kırılma, çok az yoğruk bozunum içererek ya da hiç içermeden oluşursa
gevrek kırılma olarak adlandırılır. Geçiş sıcaklığı altındaki
kırılmalar bu tür kırılmalardır. Eğer kırılmadan önce belirli bir
oranda yoğruk bozunum oluyorsa kırılma sünek kırılma diye
adlandırılır. Çekme deneylerinde görülen kırılmalarda, belverme olarak
ortaya çıkan yoğruk bozunum bardak-kapak türü kırılma biçimine yol
açar. Bir örneği Şekil II. 10'da görülen sünek kırılmada,
genellikle belverme ile birlikte başlayan yoğun yoğruk bozunum içyapı
içindeki kalıntı, çökelti v.b. parçacık sınırlarından kaynaklanan
kovukcuklar oluşturur. Bu kovukcuklar çekme uzaması ile birlikte
büyüyüp birbirleriyle birleşirler ve çekme yönüne dik bir çatlak
oluştururlar. Bu aşamada, çekme yönüne 45° eğimle ve en yüksek kesme
gerilimi doğrultusunda hızlı bir çatlak büyümesi başlar ve kesme
yanağı diye adlandırılan kırılma yüzeyleri oluşur.
Kırık yüzeylere bakıldığında, kovukcukların birleşmesi
ile oluşan bölgenin pütürlü yüzü ile sonradan oluşan ve daha düzgün
görünümlü kesme yanağı bölgesi hemen tanınabilir. Tüm sünek kırılmalar
şüphesiz tam bu anlatılan görünümde olmazlar, örneğin, birçok
menevişlenmiş çeliklerin kırık yüzeyleri incelendiğinde pütürlü bölge
ortada küçük bir alanda ve kesme yanağı bölgesi de en dışta ince bir
katman olarak görülür. Bu iki bölge, hızlı çatlak büyümesini
simgeleyen girintili çıkıntılı geniş bir arabölge ile birbirinden
ayrılır.
Sünek kırılma, genellikle, yüksek süneklik ve yüksek
tokluk özellikleri taşıyan çeliklerde görülür. Çekme dayancı ve akma
gerilimi düşük olan çeliklerde daha çok görülür.
Genellikle, tasarımda kullanılan dayanç ve süneklik
değerleri basit çekme deneyi sonuçlarından çıkarılır. Yapı
çeliklerinin uygulamada davranım biçimleri bu deneylerden elde
edilenlerden çok farklı olmamaktadır. Bu nedenle, çelik yapılarda
esnek davranım bir sorun olarak görülmez. Uygulamada, özellikle yapı
çeliklerinde karşılaşılan durum, gevrek kırılmaya yol açan
yüklemelerle doğan beklenmedik ve hızlı kırılma biçimleridir.
Gevrek kırılmada çelik kütlesi belirli kristal
yüzeylerinden yarılma gösterir ve yoğruk bozunum söz konuşu değildir.
Özellikle, hacim merkezli küp (hmk), kristalli yapılarda bu yarılma,
temel çekme gerilimine dik olarak konumlanmış küp yüzeylerinin
ayrılması ile olur (Şekil n.ll).
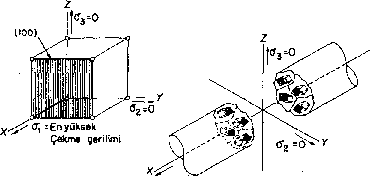
Şekil 11.11)
Gevrek Kırılmaya Yolaçan Yarılma Biçimi :
İşte, çeliklerde görülen gevrek kırılma davranımı da
çeliğin içyapısında bulunan hmk kristal yapılı ferrit evresinden
kaynaklanmaktadır. Çekme deneyinde görülen gevrek kırılmada ferritin
küp yüzeylerinden ayrılma olur. Ayrılmanın olduğu kristal yüzeylere
yarılma yüzeyler adı verilir.
Yapı çelikleri, yalın ve tek eksenel yüklemelerde, oda
sıcaklıktan ve daha yüksek sıcaklıklarda genellikle sünek davranım
gösterirler; çarpma deneyinde olduğu gibi karmaşık ve çok eksenel
yüklemelerde ve ayrıca oda sıcaklığı altındaki yalın çekme
yüklemelerinde gevrek davranıma girerler. Kırık yüzeyler
incelendiğinde deney sıcaklığının düşmesiyle yarılma kırılmasının
arttığı görülür; yapı çeliklerinin süneklik özellikleri, Şekil
11.12'de görüldüğü gibi, sıcaklık düştükçe düşmektedir. Buradan da
anlaşılacağı gibi yapı çelikleri, sıcaklık düştükçe sünek davranımdan
gevrek davranıma geçmektedirler. Ayrıca, çok eksenel karmaşık
yüklemeler ile hızlı yüklemeler gevrek davranım yaratırlar. Bu
nedenlerle, yapı çeliklerinin gevrek davranım yatkınlıkları düşük
sıcaklıklarda, çentikli numuneler kullanılarak ve çarpma yüklemeleri
altında incelenir. Tokluk özelliğinin ya da sünek davranır
yatkınlığının belirlenmesi için çarpma deneyinin kullanılması ve bunun
sonucu belirlenen geçiş sıcaklıklarını önemi buradan
doğmaktadır.
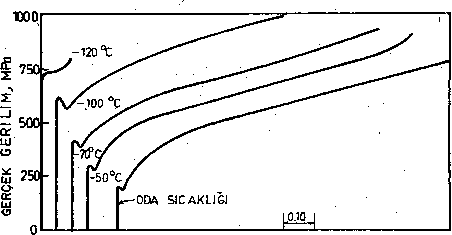
Şekil 11.12)
% 0.12 C içeren Fe- C Alaşımlarının Çekme Davranımlarının Sıcaklığa
Bağımlı Değişimi
2.3.5.3. Geçiş Sıcaklığına Etki Eden Etmenler
Tokluk özelliğünin ölçüsü olarak geçiş sıcaklığı
alınabilir. Burada geçiş sıcaklığı, anlatım kolaylığı sağlayabilme
amacıyla yalnızca Charpy geçiş sıcaklığı, Tg, olarak incelenecektir.
Tg sıcaklığının dolayısıyla da tokluk özelliği etkileyen etmenler
içyapısal ve boyutsal olarak iki ana bölüme ayrılabilir :
2.3,5.3.1. İçyapısal ya da Metalbilimsel Etmenler :
Kimyasal Bileşim: Yalın karbon çelikleri ile düşük
alaşımlı çeliklerde karbon yüzdesi arttıkça Tg çaktığı da
yükselir. Şekil 11.13'de görülen bu etki aslında içyapı
içindeki perlit-ferrit oranının% C arttıkça artmasından
kaynaklanmaktadır. Anılan şekildeki eğrilerden de görüldüğü
gibi, çeliğin bileşimindeki % C ‘nin azalması ile tavan erki, diğer
bir deyişle, çentik tokluğu da artmaktadır.
DENEY sıcaklığı.
(°C)
200 300 400
DENEY sıcaklığı,
(°K)
Şekil II.13)
Karbonun Çarpma Tokluğuna Etkisi
a) Çentik tokluğunu en çok etkileyen diğer iki element
nikel ve mangandır. Genellikle, düşük karbonlu çeliklerde Mn/C oranı
en az 3/1 olmalıdır. Bu oran arttıkça Tg, 50°C'a varan değerlerde
düşer, fakat 7/1 oranı aşılmaz. Hadfield türü yüksek manganlı yüksek
karbonlu ostenitli çelikler dışındaki çeliklerde mangan % 1.7 değerini
açmaz. Nikel, % 2 düzeyine dek, Tg sıcaklığım düşürmekte etkilidir; %
13 Ni içeren bir çelik Tg sıcaklığı göstermez
Molibden, tavlanmış çeliklerde Tg sıcaklığım düşürür,
suverilmiş menevişlenmiş çeliklerde ise Tg sıcaklığını yükseltir;
krom ise pek etkili değildir.
Silis, özellikle % 0.2 değerinin üzerine çıktığında Tg
sıcaklığını yükseltici bir etki yaratır.
Fosfor, oksijen, azot ve hidrojen çarpma yükü altında
çalışacak çeliklerin yapısında olabilecek en düşük düzeylerde
tutulmalıdır, örneğin % 0.01 P Tg sıcaklığında 7°C artış yaratır.
b) Tane büyüklüğü : Tokluk
özelliğim yansıtan Charpy geçiş sıcaklığı, Tg, ortalama tane
büyüklüğü, d, ile bileşime göre şöyle verilmektedir
:
Tg(°C)= -19+44 (%Si) + 700(Karekök(%Nf)) + 2.2 (%Perlit)-11.5 (d-1/2)
Görüldüğü gibi, tane büyüklüğü düştükçe Tg daha (—),
yani, daha düşük değerlere ulaşacaktır. Tg değerini artıran ya da
tokluğu olumsuz yönde etkileyen etmenler, yüksek Si, Nf=
(= (serbest) Özgür azot), yüksek perlit oranları ve iri
tanedir. Bu nedenle, bileşim ve tane büyüklüğü Tg sıcaklığım etkileyen
en büyük iki etmendir.
Tokluk özelliğinin yüksek istenildiği uygulamalar için
çeliğin tane büyüklüğünün küçültülmesi, perlit oranı ile çelik
bileşiminde % Si ve % N, oranlarının düşürülmesi gerekir. Bileşim
ayarlaması çelik üretim süreçleri içinde yapılır. Tane büyüklüğünün
denetimi ise çelik üretimi sırasında Al, Nb, Y ya da Ti katımlarıyla
başlar ve haddeleme işleminde düşük bitirme sıcaklıkları ile ostenit
bölgeden hızlı soğutma işlemleriyle sağlanır.
Buna Karşın bu tür çeliklerin akma
gerilimleri, o de benzer bir eşitlikle verilir.
= 15.4 [ 3.5 + 2.1 (% Mn) + 5.4 (%'Si) + 23 (%Nf)+1.13
(d-1/2) ]
Görüldüğü gibi, Tg sıcaklığım artıran, yani tokluk
özelliğim düşüren her etmen akma gerilimini de düşürmektedir. Bu
nedenle, çelik seçiminde, bu iki özellik arasında bir denge kuran
çelikler üzerinde durulur. Yapı çeliklerinin, normalleme işlemi
uygulanmış durumda, akma gerilimim her 15 MPa artıran element
katılımları Tg geçiş sıcaklığım şu değerlerde değiştirirler :
Element |
Tg sıcaklığı, oC |
P |
-53 |
N |
-30 |
Sn |
-17 |
C |
-18 |
Si |
-8 |
Mn |
-5 |
Al |
-27 |
Buradan da anlaşılacağı gibi, tokluğun yüksek
istenildiği normallenmiş yapı çeliklerinin bileşimine Al ve Mn
katılmalıdır. Tokluk özelliğinin en önemli olduğu uygulamalar için
seçilecek çeliklerin karbonu düşük, manganı yüksek (en çok % 1,5-1.7)
ve küçük taneli yapıyı oluşturmak için Al (max. % 0.75) ile oksijen
giderilmiş durgun çelikler olması gerekir. Böylece seçilecek
çeliklerde özgür azot, Al ile bağlı bulunacağından düşük
olacaktır. Fakat, silis oranının da düşük tutulması zorunludur.
Yapı çeliklerinde tokluğu artırmak için tane küçültme,
normalleme işlemi ve olası en düşük hadde bitirme sıcaklığı
uygulamasıyla da sağlanır.
c) Kalıntılar, Çeliğin içyapısı içinde yerleşmiş ve
özellikle ince uzun diziler biçiminde birikintiler oluşturmuş
kalıntılar tokluk özelliğini olumsuz yönde etkiler. MnS kalıntıları
ile Al2O3 kalıntılar özellikle levha kalınlığı
yönlerinde tokluk özelliğini çok düşürür. Bu nedenle, tokluk
özelliğinin önemli olduğu uygulamalarda kalıntı biçimini değiştirmek
amacıyla bileşimlerine Zr, Ce ya da Ca katılmış çelikler
kullanılmalıdır. Kalıntıların yoğrukluklarını etkileyen bu katımlar
Charpy tavan erkini levha kalınlığı yönünde yükseltir.
Kalıntı oluşumuna yol açan kükürt, silis ve oksijenin
çelik bileşimi içinde en düşük düzeylerde tutulması gerekir. Kalıntı
oluşumu dışında düşünülmesi gereken önemli bir etmen de birikim
oluşumudur. Kalıntı birikintilerinden başka fosfor gibi elementlerin
de birikinti oluşumu tokluğu olumsuz yönde etkiler. Tüm bu nedenlerle,
tokluk özelliği yüksek isteniyorsa % S, % P, % O, % Nf, %
S; en düşük düzeylerde tutulmalıdır.
Çeliğin bileşimindeki katışkılar (= empürite) ile
kalıntıların birleşik etkileri oksijen giderimi işlemine dayanır.
Kaynar çeliklerin oksijen içeriği yüksek olduğundan geçiş sıcaklığı
genellikle oda sıcaklığına yakın ya da onun üstündedir. Yarı-durgun
silis içerenlerinki daha düşüktür. Alüminyum ile iyice
durgunlaştırılmış çeliklerin geçiş sıcaklığı ise -50°C'a ulaşabilir.
Oksijen gidermenin V-çentikli Charpy tokluğuna etkisi Şekil 11.14'te
özetlenmektedir.
d) Çökeltiler : Çelik içyapısı içinde çökeltilerin
genel bir değerlendirmesini yapmak kolay değildir. Örneğin,
yaşlanmaya yol açan karbür ve nitrür çökeltileri tokluğu olumsuz yönde
etkiler ve Tg sıcaklığını yükseltir. Halbuki, VC gibi ostenit
evresinde kolay çözünmeyen karbürler tane küçülmesine yol
açabildiklerinden geçiş sıcaklığının yükselmesini sağlarlar.
Genellikle, çelik yapısı
|